What are composite materials?
Composites are made from two or more constituent materials, each with different properties. When combined, they create a material with properties greater than the sum of its parts. Examples include polymer, ceramic, and metal matrix composites.
Fibre-reinforced polymers (FRPs) are a subset of polymer matrix composites and the focus of our 91AV-enabled sustainable composites report.
Both strong and lightweight, FRPs are used in a wide range of industries where high-strength structures are required.
Fibre-reinforced polymer composites
FRPs are composite materials made from a thermoset or thermoplastic polymer that is reinforced with fibre, typically carbon or glass. The main advantages of FRPs are their durability, design freedom, low weight, high strength and stiffness.
Applications in industry include:
- wind turbine blades
- gas (e.g. hydrogen) and liquid tanks and pipes
- aeroplane wings, fuselage, empennage and interiors
- vehicle body panels and interiors
- roofs, pipes, cladding, window frames
- foot, road and rail bridges
- military equipment
- the hull, deck and masts of boats.
Understanding the differences between composites
Fibre-reinforced polymer composites (FRPs) consist of strong fibres embedded in a resin matrix.
When a composite is put under load each individual fibre bears a degree of that load. The resin acts to hold the fibres in position and protects them from damage and degradation (cracking, for example). The alignment of the fibre direction and overall design of the structure is, therefore, typically arranged around the desired load requirements and associated design envelope. The selection of the matrix is usually based on the environmental conditions (for example, exposure to heat, light, moisture) the application will operate within.
Thermoset | Thermoplastic | |
---|---|---|
91AV |
Crosslinking between polymer chains forms a very stable crosslinked matrix |
Weaker associations between the polymer chains rather than cross-linking bonds to form a reformable system |
Examples |
Wind turbine blades, aeroplane wings, hydrogen storage tanks |
Automotive interior trim, oil and gas pipes |
UK market share (value) in 2019 |
Epoxy = 43% Unsaturated polyester = 38% Vinyl ester = 3% Total = 84% |
Polypropylene= 9% Polyamide = 6% Other = 1% Total = 16% |
The main fibres used in composites are glass and carbon. Carbon fibre, however, has an environmental impact because of how it is made.
In addition to resins and fibres, composites contain a variety of other components, which add additional functionality such as toughening agents and coatings.
Glass fibre | Carbon fibre | |
---|---|---|
Feedstock |
Primarily derived from silica (sand) |
Can be derived from many sources but the dominant source is petrochemical derived acrylonitrile |
Production |
Glass is drawn into fibres |
Polyacrylonitrile (PAN) is drawn into fibres. Multiple processing steps remove acrylonitrile functionality and generate the highly unsaturated graphitic poly-crystalline structures which are the bulk of the ultimate fibre product |
Examples |
Wind turbine blades, boat hulls, bridges |
Wing structures, hydrogen tanks, Formula 1 car parts |
UK market share (value) in 2019 |
59% |
41% |
The major advantage of composites compared to other engineering materials, such as metals, is their strength- (and stiffness) to-weight ratio. The combination of polymer and, typically, carbon fibre used in composites have an overall lower density than engineering metals like steel and aluminium. They can, therefore, achieve the same or better mechanical performance for less weight.
The UK composites industry
The UK is a world leader in composite manufacture. In 2019, the UK composites market was worth £4 billion and is expected to reach £6.3 billion in 2035.
FRPs are widely used in aerospace, automotive, construction and infrastructure, defence, marine, oil and gas, rail, and wind. The growing hydrogen market is also expected to place significant demand on supplies of carbon fibre polymer composite.
How FRPs contribute to net zero
As well as their contribution to the UK economy, FRPs are crucial to delivering the UK’s net zero targets by 2050.
- FRPs are used in renewable energy technologies, such as wind turbine blades.
- They enable the lightweighting of transport to reduce carbon dioxide emissions.
- Their durability extends the lifetime of infrastructure.
- They are likely to be in demand for hydrogen storage and transportation.
The composites supply chain
The sourcing of materials and formulations required to manufacture composites is a global operation.
Chemical producers tend to supply raw materials to other formulators rather than directly to composites manufacturers.
In the UK, many of the raw materials used in the composite industry, such as glass and carbon fibres, are imported. For example, .
The diagram below summarises the composite supply chain and the different types of companies involved.
FRPs and sustainability
Nearly all (95%) FRPs are made from virgin materials derived from fossil fuels. While their durability means that they can be in use for many years, most FRPs end up in landfill at the end of their life.
In 2019, around 110,000 tonnes of FRPs were produced in the UK.
Those 110,000 tonnes of FRPs weigh as much as 52 London Eyes.
However, just 6% of composite material will be reused in secondary application.
6% - reclaimed and reused
94% - landfilled or incinerated
We need to move away from the current petrochemical-based linear supply chain to a more sustainable model based on a circular economy. This will mean that sustainably sourced materials are fed into a closed loop with minimal subsequent losses during manufacture and at end of life.
The current composites industry follows a linear economy
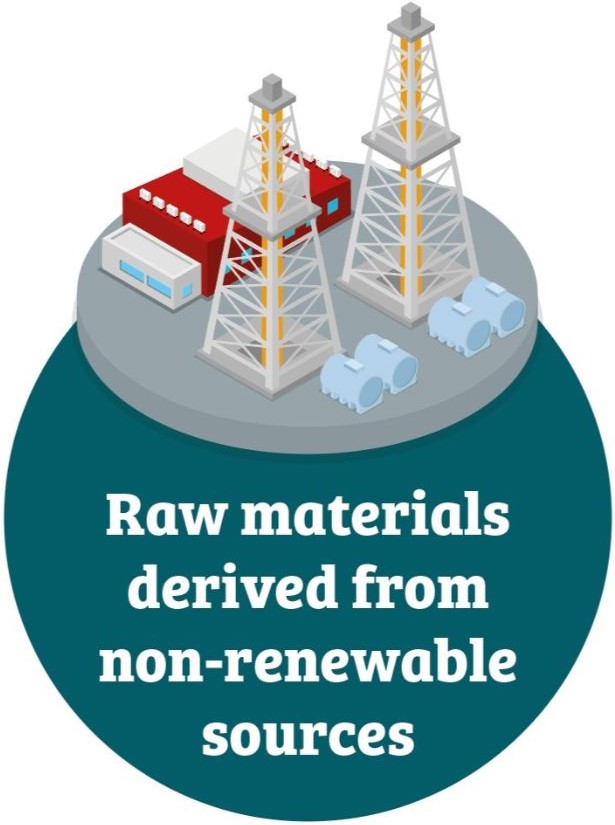

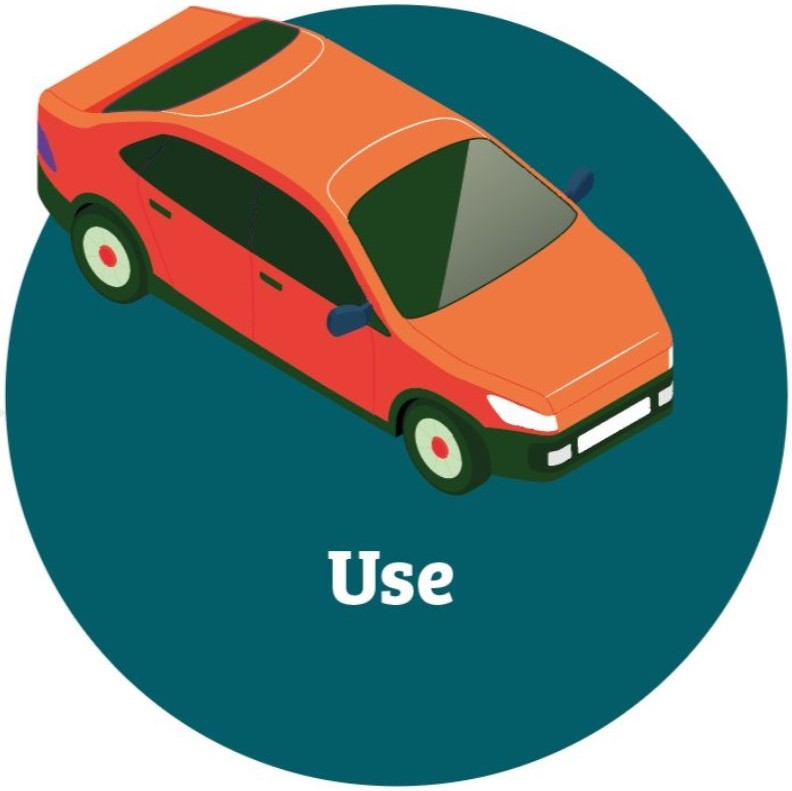

For a more detailed analysis of sustainability trends, go to section seven of our 91AV-enabled sustainable composites technical report or read our sustainability trends for composite materials page.
You may also be interested in:
Sustainability and the composites sector
The principles of sustainability and the trends and tools driving progress in this supply chain
Opportunities and case studies
Showcasing how chemistry research and innovation is enabling the development of sustainable composites
Related pages
- How can we make paint more sustainable?
- A task force of industry leaders are working with us to make polymers in liquid formulations more sustainable
- More sustainable plastics are within our grasp, but more research is needed - read our report
- Our policy on the circular economy of precious metals
- Laboratories are working to reduce the carbon footprint of their research
- Listen to our award winning podcasts covering many aspects of sustainability
- Our other environmental and sustainability work
- See all our policies, reports, evidence and campaigns
Press office
- Tel:
- +44 (0) 20 7440 3351
- Email:
- Send us an email